The Weaving of a Royal Tartan | The King Charles III Tartan
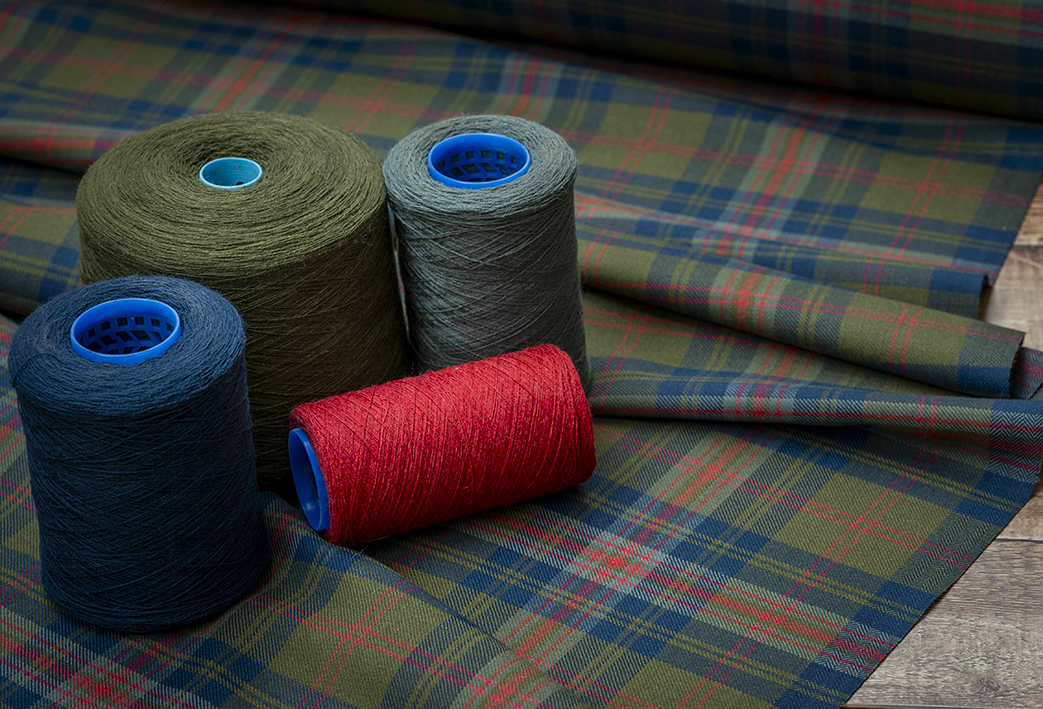
The final woven tartan with the coloured yarns used in weaving the design. Picture: Phil Wilkinson
Scotland’s rich cultural heritage is often celebrated through its traditional crafts and fabrics. One such craft is the art of weaving tartan, which holds a special place in the heart of the nation. At Lochcarron of Scotland we have been weaving tartan for generations, creating exquisite patterns and designs. Here, we explore the fascinating world of weaving a very unique tartan created for His Majesty and the significance of this timeless tradition.
HERITAGE | LOCHCARRON
Lochcarron of Scotland is a renowned Scottish weaving mill dating back to 1947. With a commitment to traditional craftsmanship and the production of premium quality authentic tartan and textiles, Lochcarron has become a global ambassador for Scottish heritage. The company offers a wide range of products, Scottish and British Wool being at the fore. Everything is meticulously crafted in Scotland, in the town of Selkirk in the heart of the Scottish Borders.
The craftsmanship involved in our tartan weaving is second to none. Each tartan is skillfully woven, and the process involves multiple stages, dyeing, winding, warping, weaving. At Lochcarron we are committed to preserving Scotland’s rich cultural heritage and are dedicated to quality and authenticity that ensures each tartan created is a piece of living history.
DESIGNING | THE KING CHARLES III TARTAN
The Scottish Tartans Authority designed the green, blue and red tartan earlier this year to mark the occasion of The Coronation and in recognition of His Majesty’s fondness of the Scottish Highlands.
The unique design presented to His Majesty, is based on the Balmoral tartan sett which dates from c.1850 and continues to be worn by The King and members of The Royal Family today. The new tartan has been officially registered with the Scottish Register of Tartans that is administered by the National Records of Scotland.
The Strome premium kilt cloth, woven in 100% Scottish wool, includes a central triple stripe motif (one broad and two narrow) which is a feature of Royal tartans previously worn by His Majesty including the Duke of Rothesay, Duke of Rothesay Hunting and Lord of the Isles Hunting tartans. The colours are matched to the natural dyes of 18th century tartan specimens in the collection of The Scottish Tartans Authority.
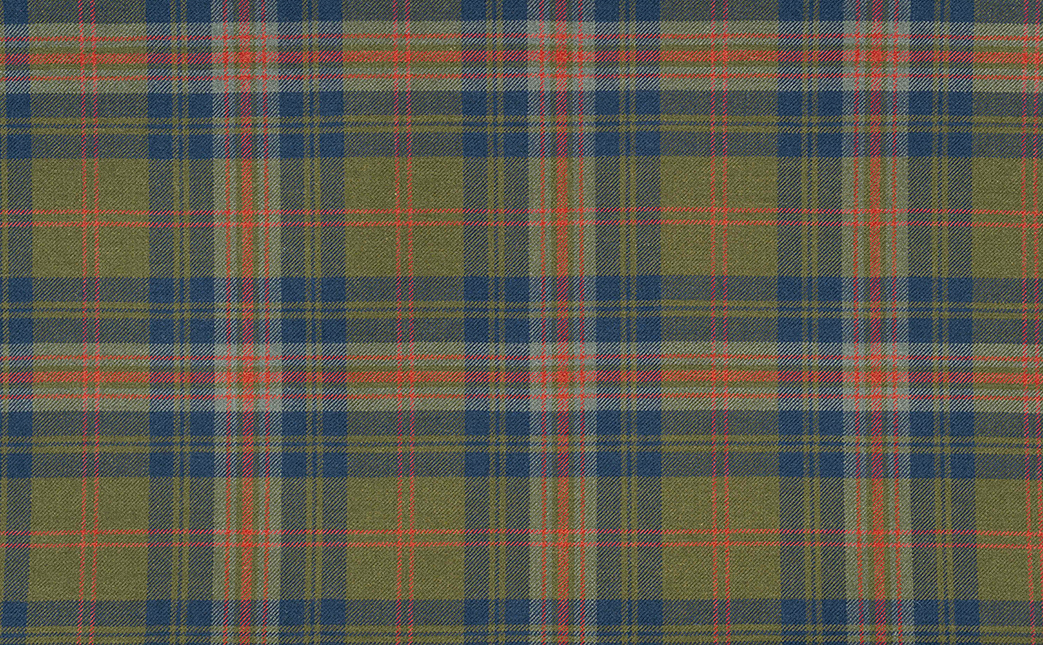
The woven tartan design. Picture: Phil Wilkinson
THE SCOTTISH TARTANS AUTHORITY
The Scottish Tartans Authority was formed as a Scottish Charity in 1995 dedicated to preserving, promoting, and protecting Scottish Tartans and Highland Dress, their respective origins, history, manufacture, use and development.
John McLeish, Chair of The Scottish Tartans Authority, said:
“Our iconic national cloth has a distinct style and evokes deep feelings of belonging, making it the best-known and best-loved fabric in the world. We are honoured that His Majesty has agreed that a new tartan should be created in his name. The King Charles III tartan now takes its place in the history books. It was a great privilege to be at Braemar to witness His Majesty wearing the tartan for the first time”
WEAVING | THE KING CHARLES III TARTAN
Weaving tartan is a meticulous and intricate process. Each design is carefully crafted to reflect its own unique characteristics.
White undyed wool is the starting point, we dye the white yarn in our dyehouse to match the approved colours for the tartan design. We use a recipe to create the correct quantity of dyestuffs and colours to create the shades which are mixed with water and fed into the dyepot. The mixture is pumped by perforated rods through the yarn, which have been wound onto springs to allow the dye liquor to perforate through the yarn to give a level dyeing. Once the yarns are dyed and dried, they are organised for weaving. The yarn is fed into the warp creel in the correct order for the pattern design and to the required length. The ends of the yarn are then passed through the reed to comb the yarn, removing any knots. While maintaining a uniform tension and density of the yarn, the warp threads, now a sheet of uniformly spaced yarn, are wound onto the warping drum.
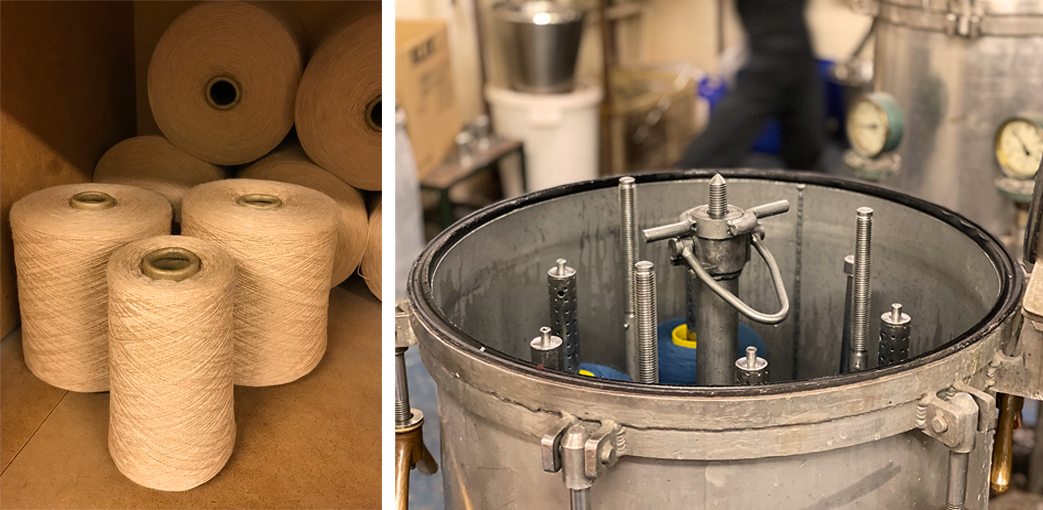
Undyed yarn (left) and yarn in the dyepot (right), after dyeing.
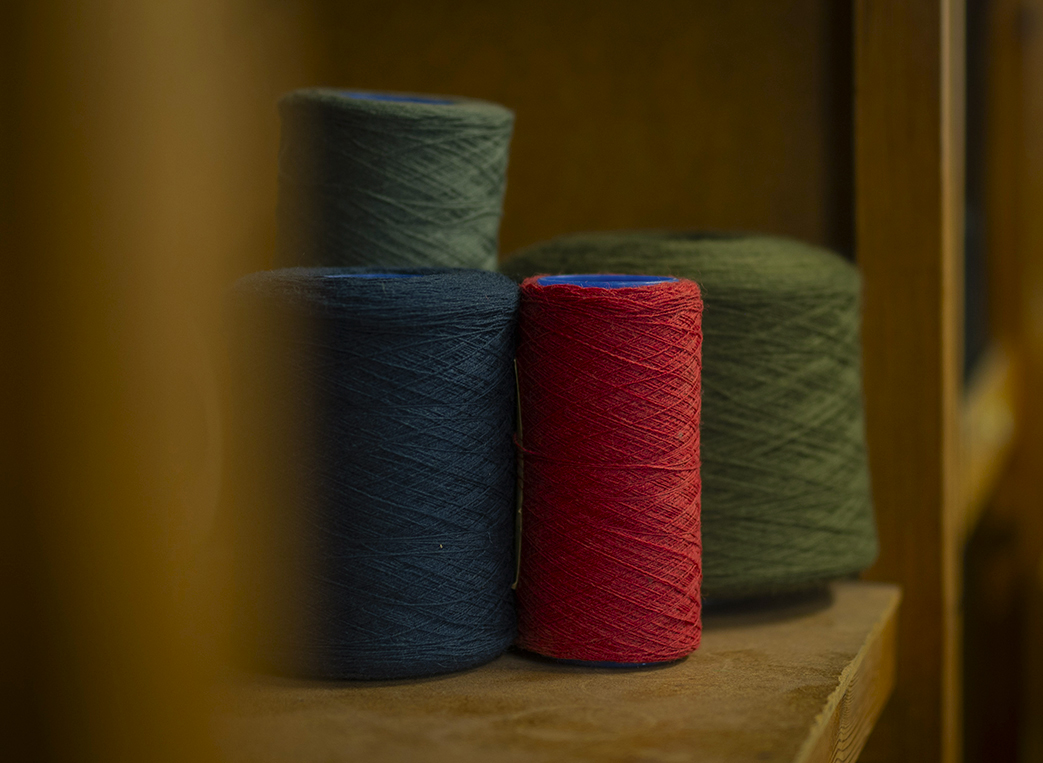
The four colours of dyed yarn used in weaving the King Charles III tartan. Picture: Phil Wilkinson.
When warping is complete, the warp is tied and transferred onto the beam. The warp is then fixed in the back of the loom where the beam can rotate freely and supply the warp to the front of the loom. Each single warp thread is drawn in through the eye of the wire heddles in the shafts, which move to create the interlacings in the structure. During the weaving process, the shafts and threads are lifted and lowered in the order that they have been fed through the heddles, determining how the weft yarn interlaces with the warp to create the woven fabric. Therefore, the pattern must be followed carefully to ensure there are no mistakes. Once the warp is set up on the loom, the rapier can transport the weft yarn across the warp, allowing it to interlace with the warp threads to create woven fabric. The first 30 cms of every order produced are checked and approved before weaving progresses. A facemark is inserted to indicate the face of the cloth. Everything woven at Lochcarron is inspected by our darners to ensure that the pattern, the colours and the weave (the construction of the cloth) is correct. Any faults are mended, knots are pulled to the back and in scarves, opened and threaded into the woven construction. We darn at this stage when the construction is quite open and before the cloth is finished. When the final fabric is complete, it is then sent to the finishers where it will move through different wet and dry processes until the final quality is achieved, ensuring the fabric is fit for purpose.
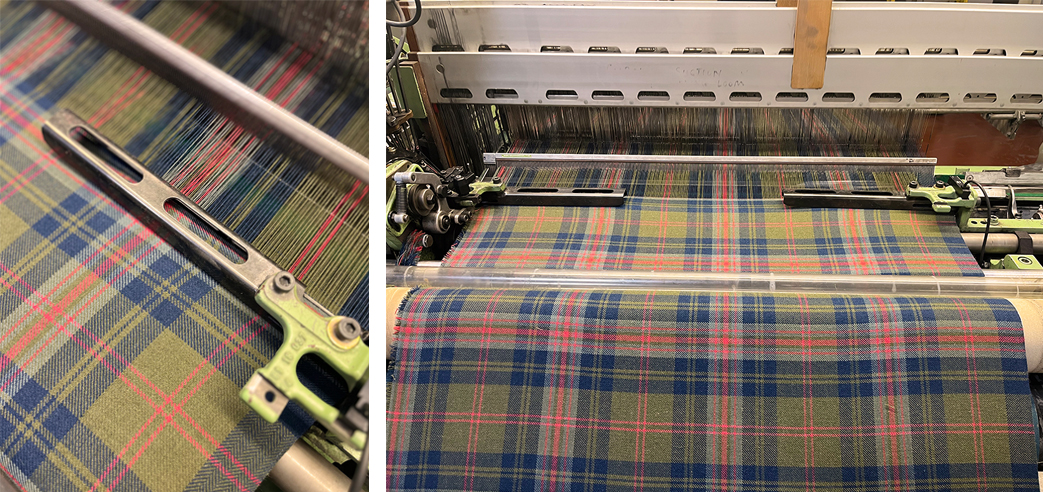
Weaving the tartan on the specially adapted single-width loom.
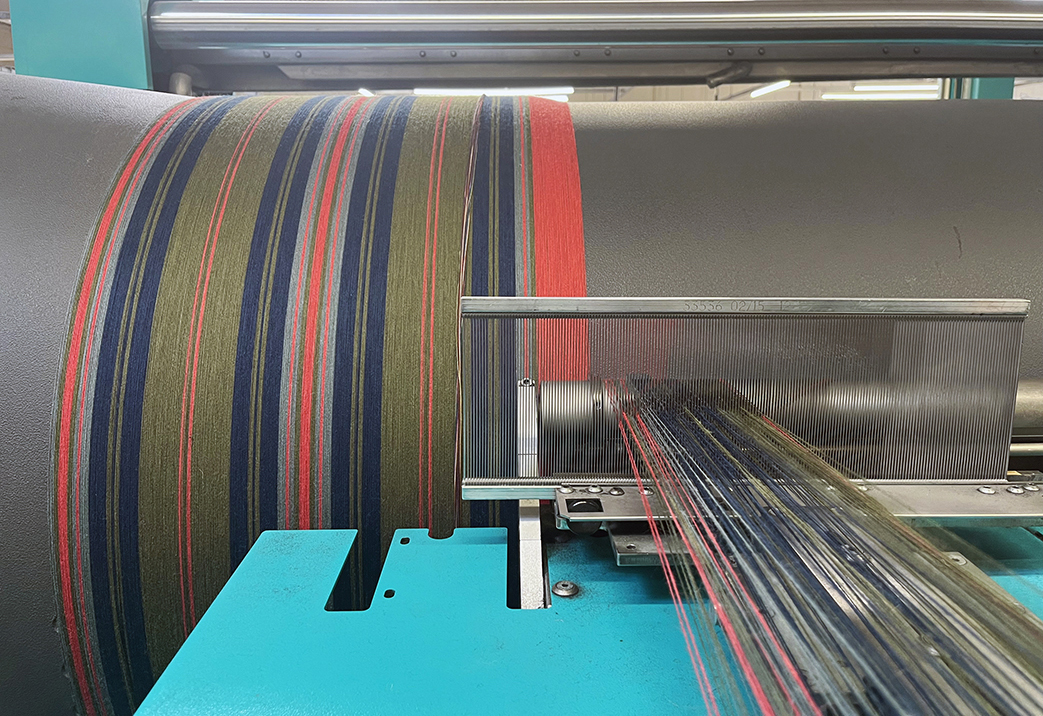
Winding the warp onto the warping drum.
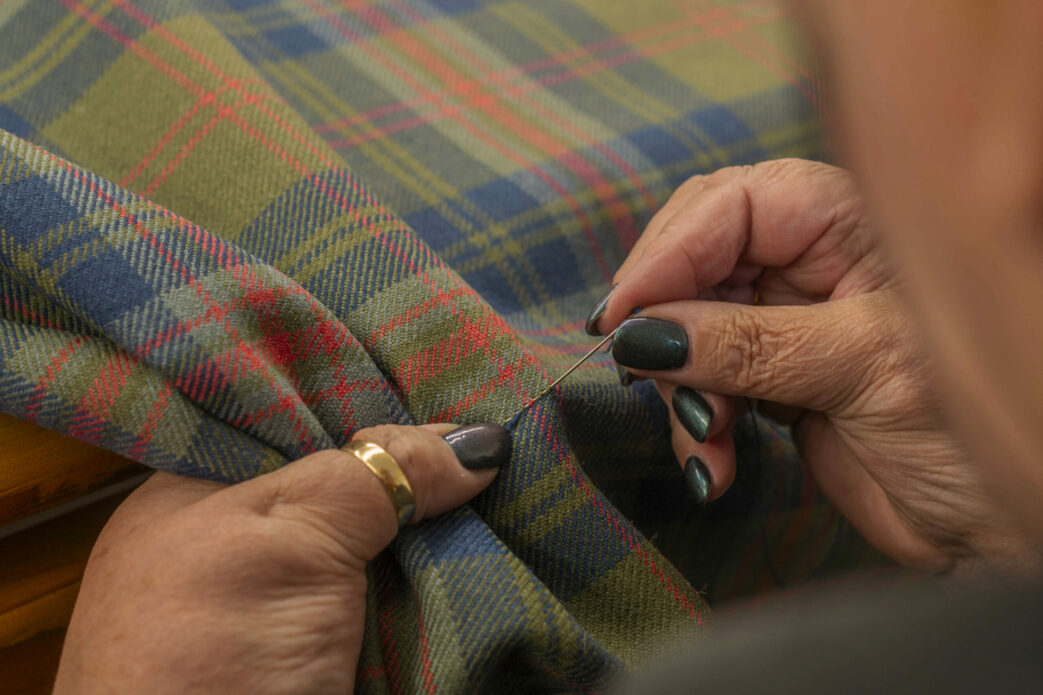
Darning the woven cloth. Picture: Phil Wilkinson
The King Charles III tartan is made in our premium heavy-weight Scottish wool Strome cloth. Strome was finally decided upon as the most suitable due to several factors, the main considerations being, this quality of fabric is woven in 100% Scottish wool, the other the use of the specially adapted single-width loom which is capable of reproducing historical details particularly, within the selvedge, or kilt edge. This is a traditional finished edge that is found at the bottom of a kilt. This is not hemmed but created by weaving with a weft thread that moves back and forth across the warp/width continuously, turning on the warp edge in such a way that binds the edges of the cloth perfectly which prevents unravelling. As the sett included a traditional herringbone selvedge, only this was the ideal loom to be used to produce the fabric. Once the kilt was produced the selvedge would be located at the bottom of the kilt, creating a subtle but bespoke woven detail. A further advantage of the herringbone selvedge is that it creates a slightly thicker edge and is more freeing, giving the fabric flow and movement. This characteristic was often found on rural Highland cloth from the 18th century, however with the development of mass production in the early 19th century, was no longer incorporated and is unusual to find today.
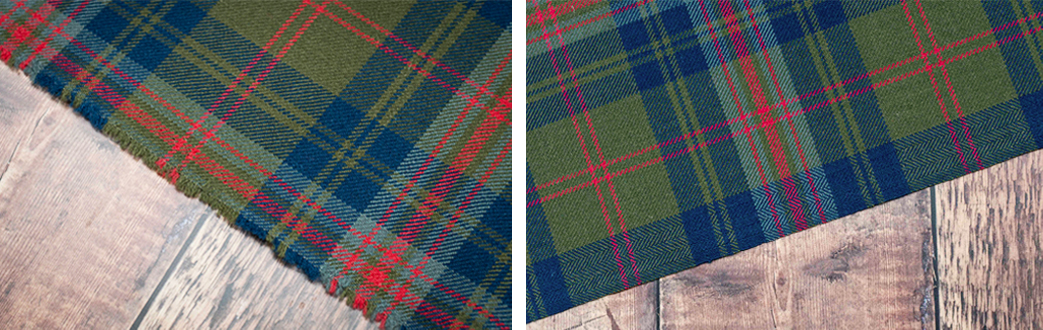
Close up of each edge of the fabric for comparison, the unfinished edge (left) and the herringbone selvedge (right). Pictures: Phil Wilkinson
The Scottish yarn is a blend of wool from the Cheviot and Romney Marsh sheep. The wool is sourced solely in Scotland, through the British wool depot in Selkirk, giving us regional traceability to wool grown on our doorstep. This supports our ethical and sustainable journey in using responsibly sourced wool, and in championing British and Scottish farmers. The Scottish wool also helps in combination with simple finishing to give the cloth a traditional handle of a tartan woven before the 1950s.
Our role involved helping to prepare for the process of weaving the cloth, working with the Scottish Tartans Authority, we were provided with the artwork, thread counts and colours from the design concepts.
A key aim of the project was to closely represent cloth from the 18th century, it was important that the colours replicated the softer hues from traditional natural dyes of this time. Therefore, it was necessary that the colours from the artwork designs on CAD (Computer Aided Design) were matched exactly with the shade of yarn. The shades in the King Charles III tartan were influenced by tartan specimens from the 18th century located within The Scottish Tartans Authority's collection.
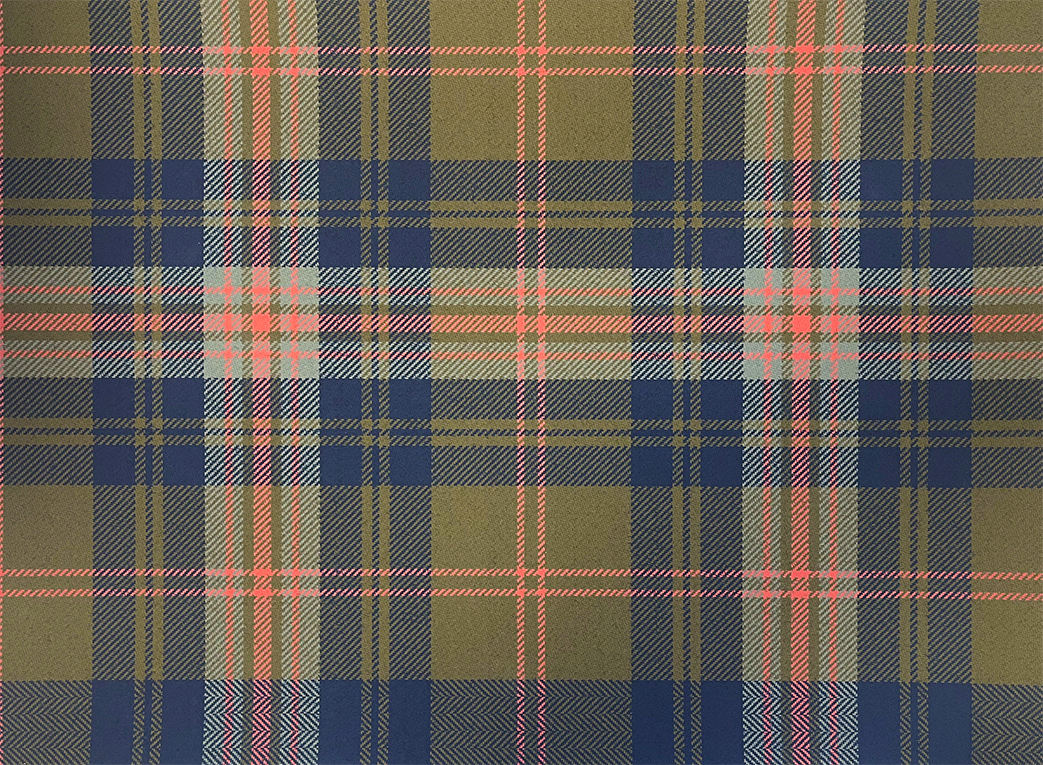
CAD image of the final design.
Different layout options with the chosen colours were also edited on CAD. These options were then shown by the Scottish Tartans Authority to His Majesty, who has been involved and consulted throughout the journey of this tartan, His Majesty made the final design selection.
Heritage was of key prominence within the design process and therefore important to incorporate traditional features of royal tartans. The pattern was influenced by royal tartans which feature a central stripe motif (one broad and two narrow) that have been worn previously by His Majesty, including the Duke of Rothesay Hunting tartan which he wore when he visited Lochcarron of Scotland on the 6th of July 2023. During his visit, the King was able to see first-hand the tartan designed for him weaving on the loom and engage with the skilled craftspeople responsible for producing the tartan.

Their Majesties King Charles and Queen Camilla arriving at Lochcarron of Scotland in July 2023 and the King viewing his tartan being woven in our mill. Pictures: Phil Wilkinson
The final woven fabric was to be made into a kilt therefore the sett and the pattern repeat size were carefully considered to ensure the design pattern for the front of the kilt would be perfect.

The final woven fabric. Pictures: Phil Wilkinson
The King Charles III tartan made its first public appearance when King Charles III wore his new kilt at the Braemar Gathering on Saturday 2nd Of August 2023.
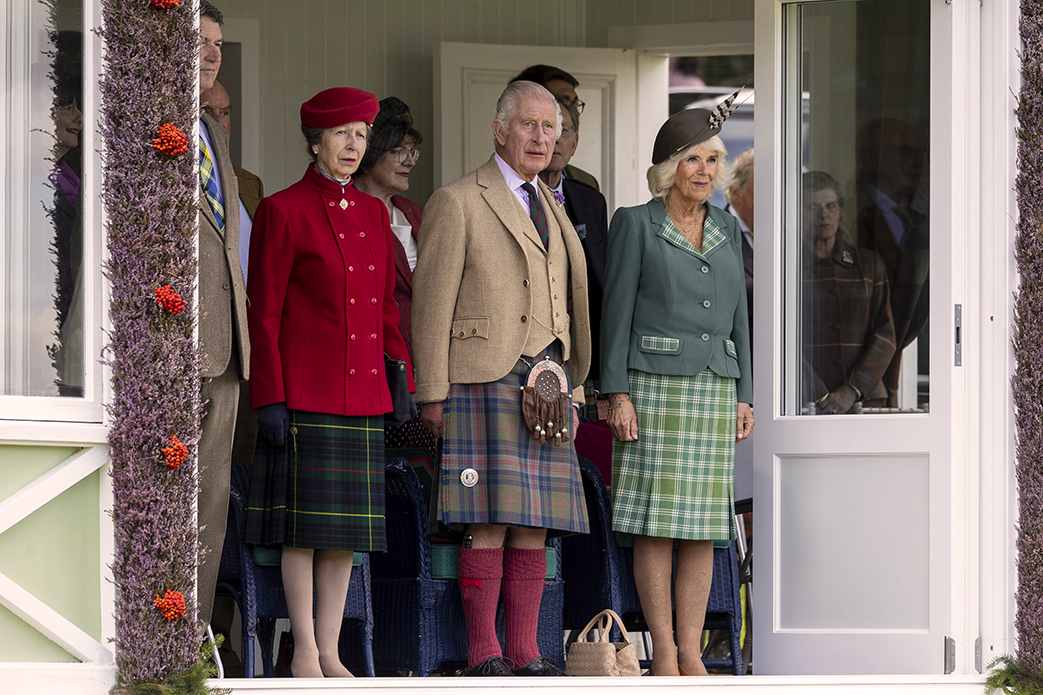
Braemar Gathering 2023 Aberdeenshire Scotland. Picture: Derek Ironside / Newsline Media